Understanding Concrete Batching Plants: The Backbone of Construction Industry
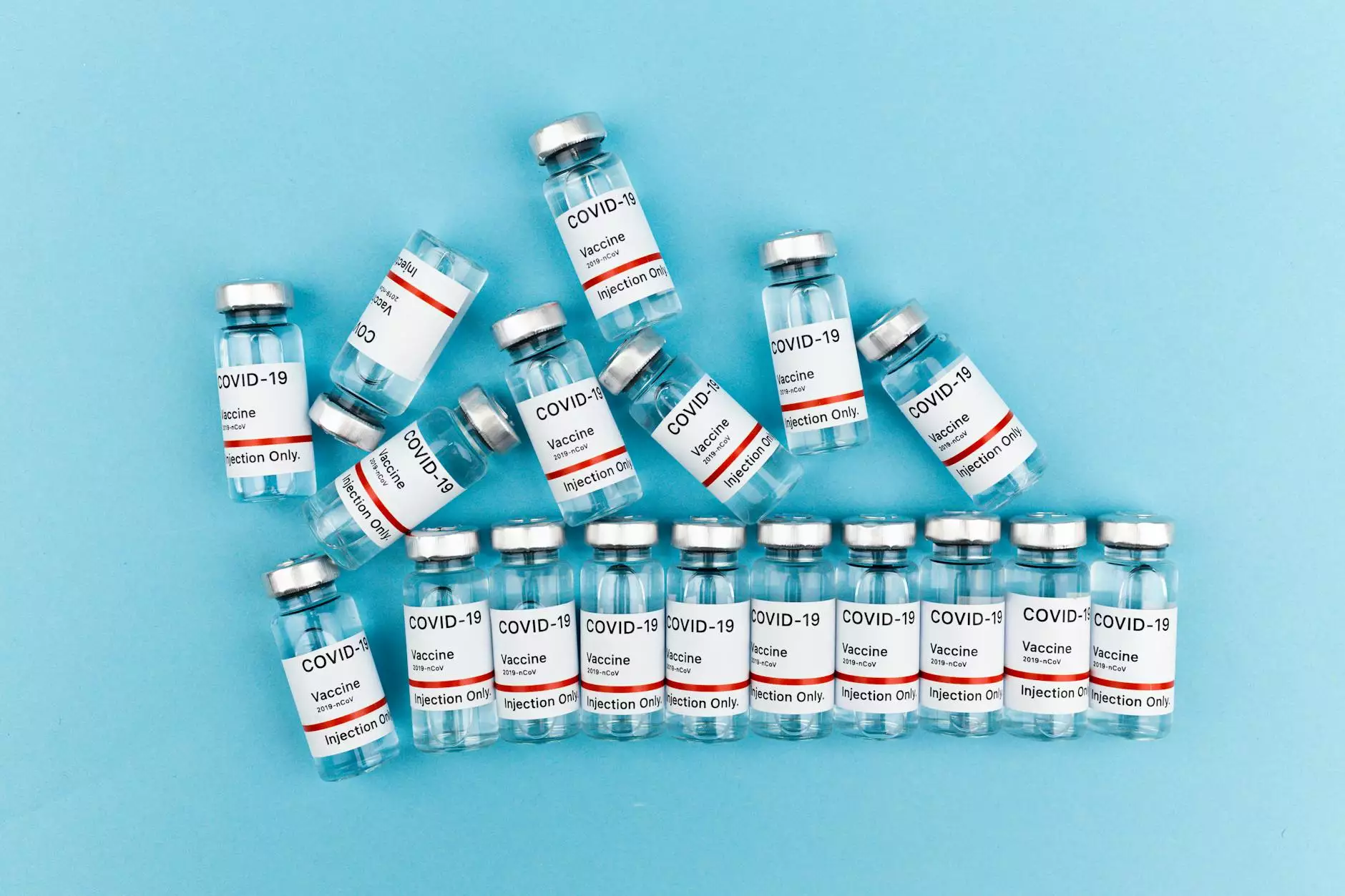
In the vast landscape of modern construction, concrete batching plants play a critical role that cannot be overstated. Whether you're building skyscrapers, bridges, or roads, the efficiency and quality of concrete are paramount, and these facilities ensure both. In this article, we will delve deep into what concrete batching plants are, their types, how they operate, their advantages, and their significance in the ever-evolving construction industry.
What is a Concrete Batching Plant?
A concrete batching plant is a facility that combines various ingredients to form concrete. These ingredients typically include cement, water, sand, aggregates, and sometimes additives. The process of batching can be automated or manual, and it ensures that the final mixture meets precise specifications for quality and performance.
The Importance of Concrete Batching Plants
Concrete batching plants are vital for several reasons:
- Quality Control: They ensure that concrete is mixed to exact specifications, resulting in high-quality construction materials.
- Efficiency: Automated batching minimizes waste and maximizes resource use, contributing to faster project completion.
- Consistency: Regular production of concrete allows for uniformity in construction projects, essential for structural integrity.
- Versatility: They can produce various types of concrete needed for different applications, from standard concrete to specialized mixes.
Types of Concrete Batching Plants
Concrete batching plants can primarily be categorized into two types:
1. Stationary Concrete Batching Plant
This type is installed permanently at a construction site and is ideal for large projects that require a significant amount of concrete over an extended period. Stationary plants have large production capacities and can deliver consistent quality. They are designed for high output and can produce concrete that meets various specifications.
2. Mobile Concrete Batching Plant
Mobile plants offer flexibility and convenience, as they can be easily transported between job sites. These are best suited for projects with lower concrete requirements or those that are spread out geographically. Mobile concrete batching plants allow for on-site mixing, reducing transportation costs and time.
How Concrete Batching Plants Operate
The operation of a concrete batching plant generally follows these steps:
- Weighing: The first step involves weighing all raw materials according to predetermined specifications. Precise measurements ensure quality.
- Mixing: After weighing, the materials are mixed in a concrete mixer. This can be a pan mixer, twin-shaft mixer, or another type, depending on the design of the plant.
- Discharging: The mixed concrete is discharged into transport vehicles or storage for immediate use or curing.
Advantages of Using Concrete Batching Plants
There are numerous advantages associated with the use of concrete batching plants:
- Improved Material Quality: By controlling ingredient ratios and mixing processes, batching plants produce higher quality concrete compared to manual mixing methods.
- Minimized Waste: Automated systems reduce material waste and enhance economical resource use.
- Lower Labor Costs: Automation reduces the need for manual labor, significantly lowering overall project costs.
- Fast Turnaround: With quick batching and high output, projects can progress more rapidly, preserving timelines and budgets.
Maintenance of Concrete Batching Plants
Maintaining a concrete batching plant is crucial for operational efficiency and longevity. Regular checks and maintenance tasks typically include:
- Daily Inspections: Visual inspections for any obvious wear and tear, lubricant levels, and the general condition of machinery.
- Routine Cleaning: Keeping the mixers and hoppers clean to prevent material buildup and ensure consistent mixing.
- Lubrication: Regular lubrication of moving parts to minimize friction and wear.
- Calibration: Periodic calibration of weighing and mixing systems to ensure accuracy.
Regulations and Compliance in Concrete Batching
Concrete batching plants must adhere to several regulatory standards, including:
- Environmental Regulations: Compliance with local environmental laws to minimize noise, dust pollution, and waste management.
- Safety Standards: Ensuring workplace safety for employees handling materials and operating equipment.
- Quality Standards: Meeting National and International Quality standards, which include specifications set forth by organizations such as ASTM and ACI.
Future Trends in Concrete Batching
The concrete batching industry is evolving with modern technology. Here are some trends to watch for:
- Automation and AI: The use of artificial intelligence and advanced automation is increasing efficiency and precision.
- Sustainability: Plants are now focusing on sustainable practices, including the recycling of concrete and using eco-friendly materials.
- Integration with IoT: The Internet of Things (IoT) is beginning to play a significant role in monitoring and managing batching processes for optimal operations.
Conclusion
In the intricate world of construction, concrete batching plants serve as the backbone ensuring that high-quality concrete is readily available for various projects. Understanding their operation, advantages, maintenance, and trends can empower business owners and project managers alike to make informed decisions. Whether it is through a stationary or mobile setup, the incorporation of modern technology into batching processes signifies a bright future for concrete batch production. Investing in high-quality batching equipment from reputable companies like Polygonmach can set a foundation for success in any construction endeavor.