Die Casting Automotive: Revolutionizing Metal Fabrication
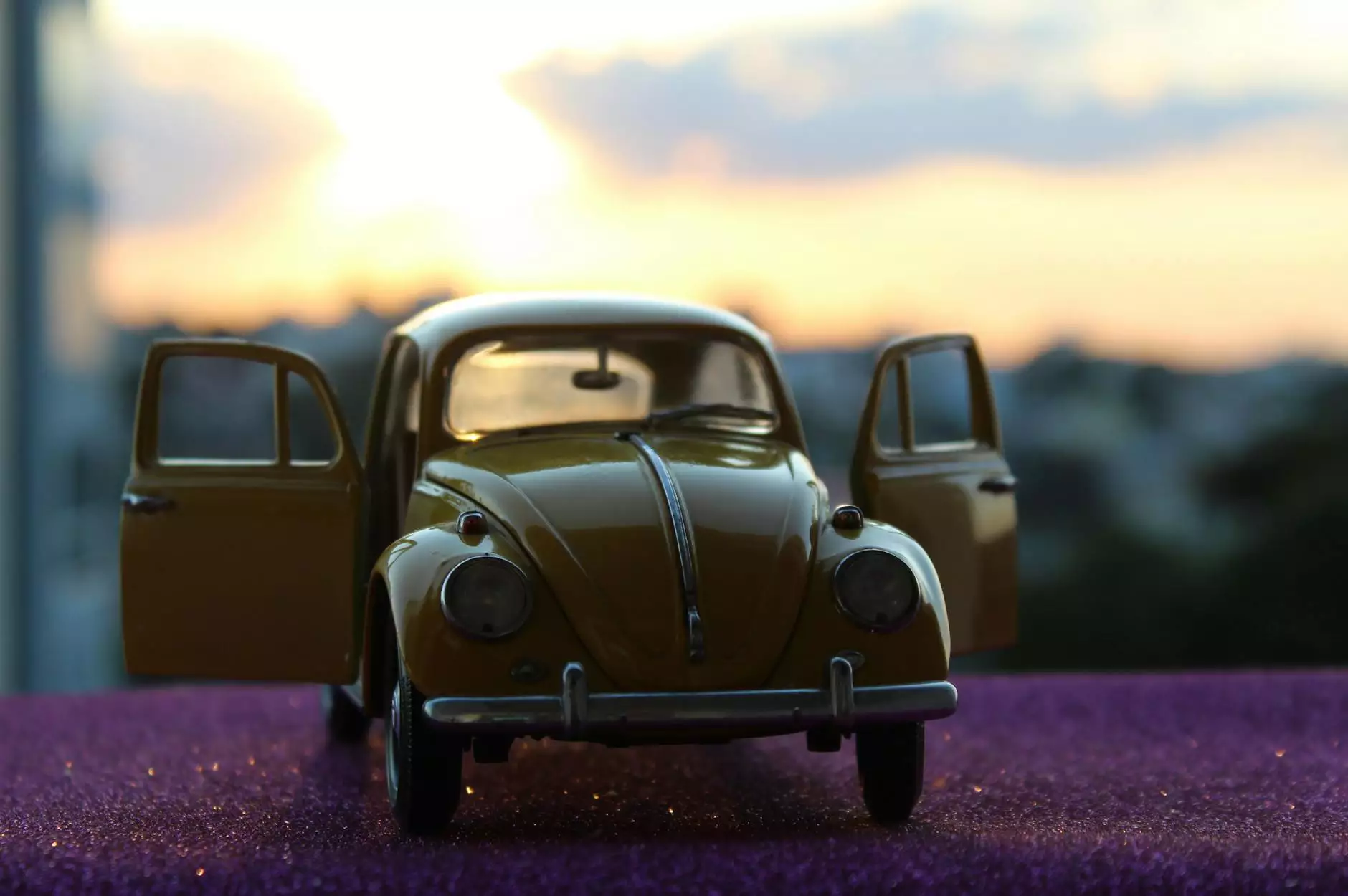
In today's fast-paced automotive industry, the demand for high-quality, efficient, and innovative manufacturing processes is greater than ever. One of the standout processes that has helped fuel this revolution is die casting automotive. This technique not only enhances the quality and durability of automotive parts but also contributes to significant cost savings and production efficiencies. In this comprehensive article, we delve into the intricacies of die casting in the automotive sector, exploring its benefits, applications, and impact on the future of metal fabrication.
What is Die Casting?
Die casting is a manufacturing process that involves forcing molten metal under high pressure into a molded cavity. The mold, often made of hardened steel, is designed to create a specific shape. Once the metal cools and solidifies, the mold is opened to reveal the finished part. The dies used are engineered for durability and precision, making die casting an ideal choice for creating complex shapes and designs in a variety of metals.
The Advantages of Die Casting in Automotive Manufacturing
Die casting has gained popularity in the automotive industry for several compelling reasons:
- High Precision: Die casting produces parts with excellent dimensional accuracy and surface finish, reducing the need for extensive machining.
- Rapid Production: The quick turnaround time of die casting allows manufacturers to meet market demands swiftly.
- Cost Efficiency: By minimizing waste and optimizing material usage, die casting leads to lower production costs over time.
- Material Versatility: Various metals, including aluminum, zinc, and magnesium, can be used in the die casting process.
- Complex Geometries: Die casting can create intricate shapes that may be difficult or impossible to achieve with other manufacturing techniques.
Key Materials Used in Die Casting
The choice of material is critical in the die casting process. For the automotive sector, the following materials are most commonly utilized:
Aluminum
Aluminum die casting is favored for its light weight and resistance to corrosion. Components made from aluminum can help improve fuel efficiency and overall vehicle performance.
Zinc
Zinc is another popular choice due to its strength, dimensional stability, and excellent surface finish. It is ideal for intricate designs and small parts.
Magnesium
Magnesium die casting offers a high strength-to-weight ratio, making it particularly useful for weight-sensitive automotive components, such as chassis elements.
Applications of Die Casting in the Automotive Industry
Die casting plays a crucial role in various automotive applications. Here are some key areas where it is utilized:
Engine Components
Die casting is frequently used to produce components like engine blocks, cylinder heads, and transmission cases, which require high precision and strength.
Structural Parts
Parts such as brackets, housings, and support structures benefit from die casting's ability to create complex shapes while maintaining strength.
Exterior Accessories
Die-cast components are often used in exterior automotive features such as grilles, mirrors, and other decorative elements that also require durability.
The Die Casting Process: A Step-by-Step Guide
The die casting process involves several steps to ensure the creation of high-quality automotive components:
- Melting: The chosen metal is melted in a furnace until it reaches a specific temperature.
- Injection: The molten metal is injected into the die at high pressures, ensuring it fills all cavities.
- Cooling: Once injected, the metal is allowed to cool and solidify within the die.
- Die Opening: The die is opened to release the finished component.
- Trimming: Any excess material, known as flash, is trimmed off to achieve the final specifications.
Environmental Considerations in Die Casting
As industries worldwide strive for sustainability, die casting is evolving to minimize its environmental impact. Efforts include:
Recycling Metal
Many die casting manufacturers focus on recycling scrap metal from the production process, significantly reducing waste and conserving natural resources.
Energy Efficiency
Innovations in furnace technology and automation help decrease energy consumption during the die casting process, contributing to a lower carbon footprint.
Future Trends in Die Casting Automotive
The future of die casting in the automotive sector looks promising, with advancements in technology driving innovation:
Automation and Robotics
Increased use of automation allows manufacturers to streamline the die casting process, enhancing efficiency and reducing labor costs.
3D Printing in Die Casting
Integrating 3D printing with die casting processes allows for rapid prototyping and the creation of customized components with complex designs.
Why Choose Deep Mould for Die Casting Automotive Solutions?
At Deep Mould, we pride ourselves on delivering exceptional die casting solutions tailored to meet the diverse needs of the automotive industry. Our commitment to quality, precision, and customer satisfaction sets us apart. Here’s why we are the preferred choice:
- Expertise: Our team comprises skilled professionals with extensive experience in die casting.
- State-of-the-art Technology: We employ advanced die casting machinery to ensure high-quality production.
- Customer-Centric Approach: We work closely with our clients to understand their specific requirements and deliver tailored solutions.
- Commitment to Sustainability: Deep Mould actively implements eco-friendly practices in our operations.
Conclusion
In conclusion, the process of die casting automotive is a vital aspect of the modern automotive industry. Its ability to produce precise, durable, and lightweight components makes it indispensable. As automotive technology continues to evolve, die casting will play an increasingly significant role in achieving efficiency and sustainability. For businesses looking to leverage the advantages of die casting, partnering with experienced providers like Deep Mould will ensure access to top-tier solutions that meet the evolving demands of the automotive market.